Вот и привез я трубку и радиатор.
Трубка оригинал с датчиком идет.
Радиатор Nissens. за все заплачено 7т.р.
Итак.
Снимаем фары.
Снимаем бампер, 4 торкс сверху по 3 на арках под крыльями и 3 крепежа снизу(как правильно назвать не знаю заглушки в середине каждой стержень, при выдавливании которого заглушка легко вынимается).
далее снял металлическую балку спереди по 3 больших торкс с каждой стороны.
Трубка справа была уже снята заранее там тряпочка воткнута.
Трубка слева, та что раненая )) снимаем ,для того чтоб разомкнуть трубки использовал кусок трубы металопласт на 15 вроде на фото все видно.
Итак далее откручиваем 4 болта крепления радиатора и и и он не выходит)), чтоб не разбирать ничего больше и вынуть его я сделал пропилы справа в местах, где он(радиатор крепится(на фото видно).Ну вот я его и снял. под ним не очень то и грязно на мой взгляд.
Грязь с основного радиатора смахнул...
И вот уже поставил новый..
Скажу сразу радиатор не идеален, поэтому без небольшого колхоза не обошлось. Три точки крепления встали в одну плоскость, а четвертая отходит на мм на 6-7, поэтому чтоб не тянуть и не напрягать новый радиатор я решил лучше подложить в это пространство гайку ее не видно, а гайка что видна подложена тк тот саморез что был стал короток, а тот что я нашел длинный, и вот именно для того чтоб не перетянуть подложил гайку и снаружи.))
Ну вот вроде и все собираем в обратной последовательности.Кидаю несколько фоток по сборке.
К сожалению не все резинки поменял тк пришли сцуко не те что заказывал.
и главное заправлю я его только завтра, так что зря я потратил деньги и время или нет я еще не знаю.Результат отпишу конечно же.К тому же я если будет все гудд хочу сделать антибактериальную обработку и сразу поменяю салонный фильтр.
Кстати мне кажется я нашел место утечки(возможное).Руки чесались и я решил посмотреть на осушитель. Так вот крышеску круглую люминовую под которой он еле вынул она в ужасном состоянии почти прогнила вся в коррозии резинки все в коррозии( вот я и подумал, что возможно тут и сочилось).
Осушитель разобрал. По моему он 2002года рождения. Кто спец скажите в каком состоянии должен быть селикогель(ведь это он я так понимаю?).
вот крышка только очень плохое фото(
Все, спасибо за внимание, завтра напишу как все заработало, или не заработало))
Трубка оригинал с датчиком идет.
Радиатор Nissens. за все заплачено 7т.р.
Итак.
Снимаем фары.
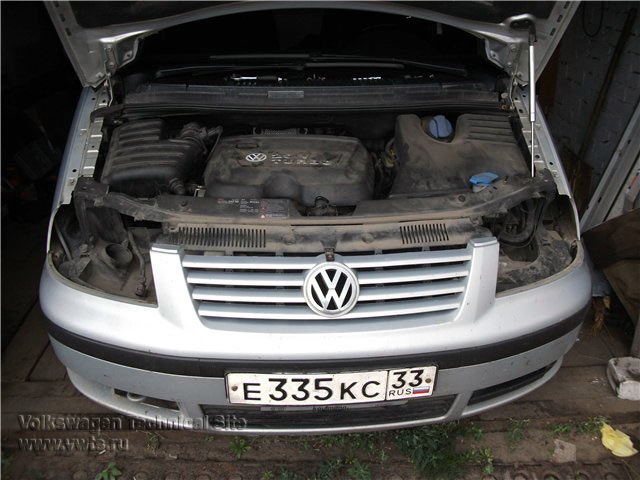
Снимаем бампер, 4 торкс сверху по 3 на арках под крыльями и 3 крепежа снизу(как правильно назвать не знаю заглушки в середине каждой стержень, при выдавливании которого заглушка легко вынимается).
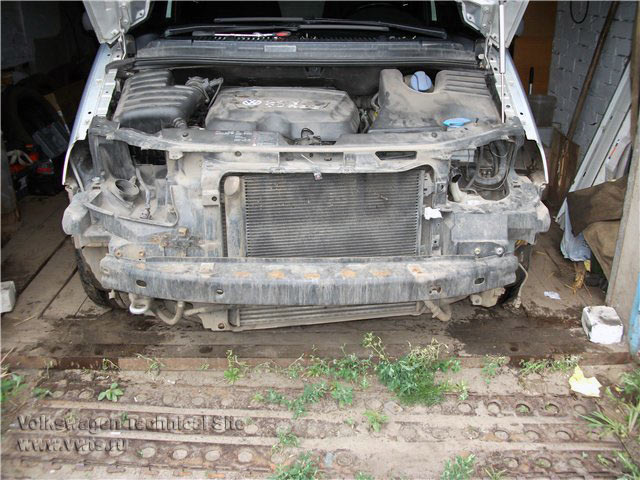
далее снял металлическую балку спереди по 3 больших торкс с каждой стороны.
Трубка справа была уже снята заранее там тряпочка воткнута.
Трубка слева, та что раненая )) снимаем ,для того чтоб разомкнуть трубки использовал кусок трубы металопласт на 15 вроде на фото все видно.
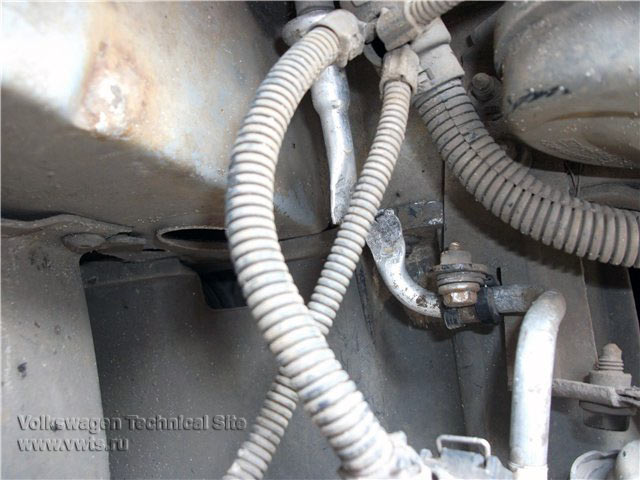
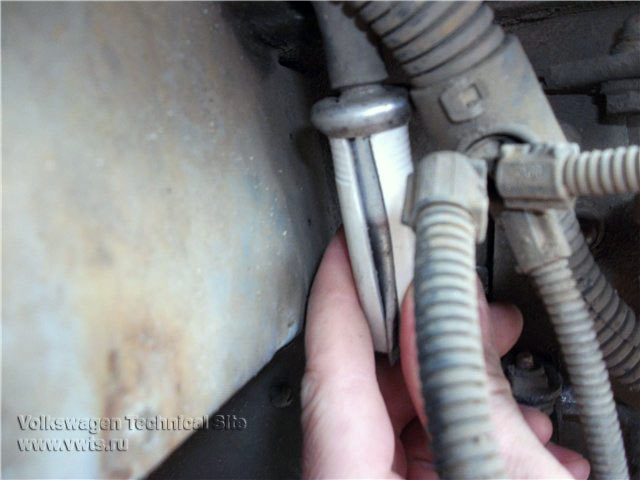
Итак далее откручиваем 4 болта крепления радиатора и и и он не выходит)), чтоб не разбирать ничего больше и вынуть его я сделал пропилы справа в местах, где он(радиатор крепится(на фото видно).Ну вот я его и снял. под ним не очень то и грязно на мой взгляд.
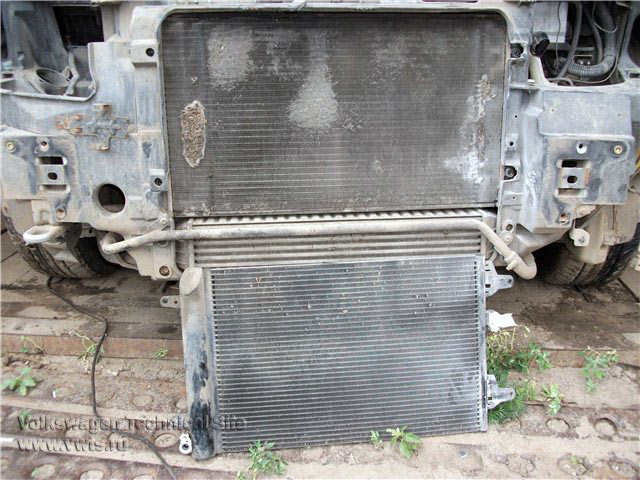
Грязь с основного радиатора смахнул...
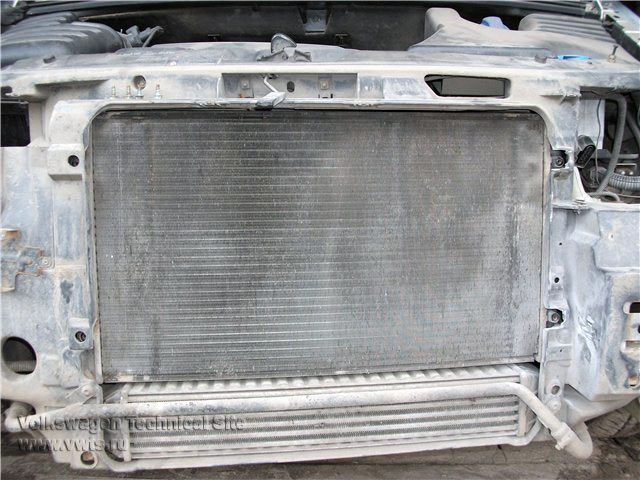
И вот уже поставил новый..
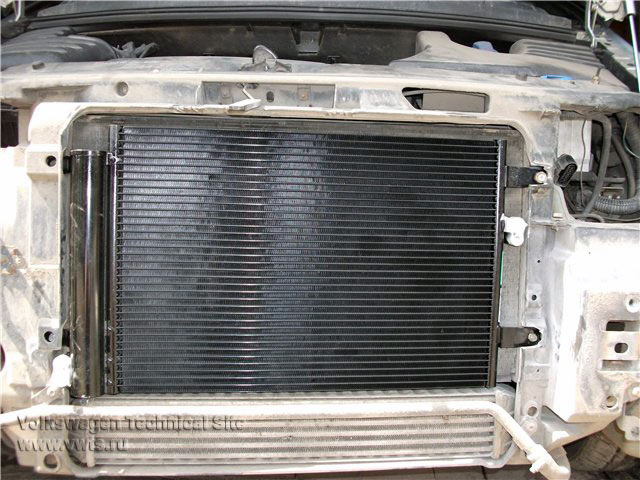
Скажу сразу радиатор не идеален, поэтому без небольшого колхоза не обошлось. Три точки крепления встали в одну плоскость, а четвертая отходит на мм на 6-7, поэтому чтоб не тянуть и не напрягать новый радиатор я решил лучше подложить в это пространство гайку ее не видно, а гайка что видна подложена тк тот саморез что был стал короток, а тот что я нашел длинный, и вот именно для того чтоб не перетянуть подложил гайку и снаружи.))
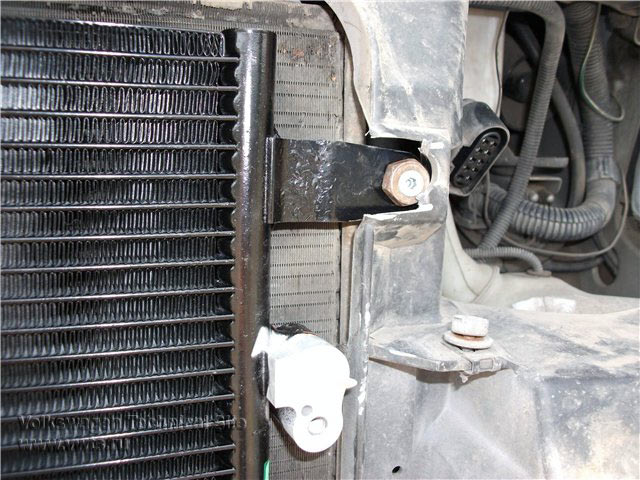
Ну вот вроде и все собираем в обратной последовательности.Кидаю несколько фоток по сборке.
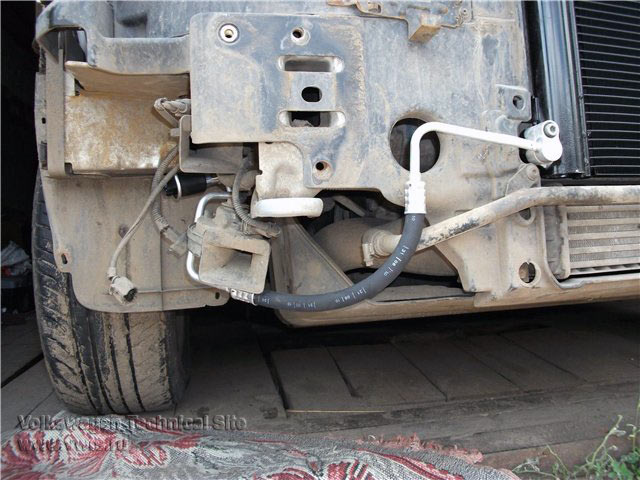
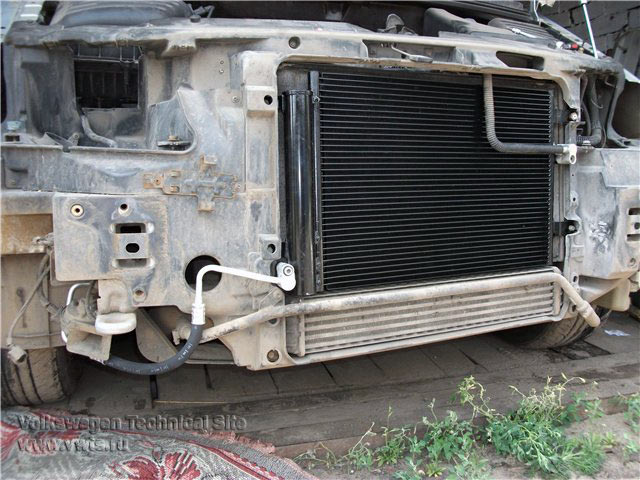
К сожалению не все резинки поменял тк пришли сцуко не те что заказывал.
и главное заправлю я его только завтра, так что зря я потратил деньги и время или нет я еще не знаю.Результат отпишу конечно же.К тому же я если будет все гудд хочу сделать антибактериальную обработку и сразу поменяю салонный фильтр.
Кстати мне кажется я нашел место утечки(возможное).Руки чесались и я решил посмотреть на осушитель. Так вот крышеску круглую люминовую под которой он еле вынул она в ужасном состоянии почти прогнила вся в коррозии резинки все в коррозии( вот я и подумал, что возможно тут и сочилось).
Осушитель разобрал. По моему он 2002года рождения. Кто спец скажите в каком состоянии должен быть селикогель(ведь это он я так понимаю?).
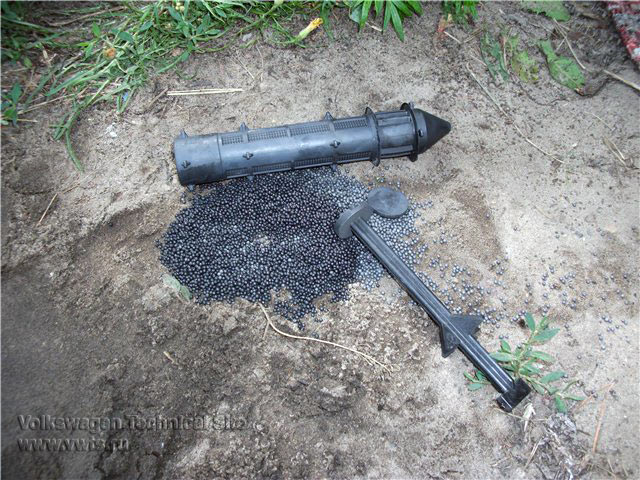
вот крышка только очень плохое фото(
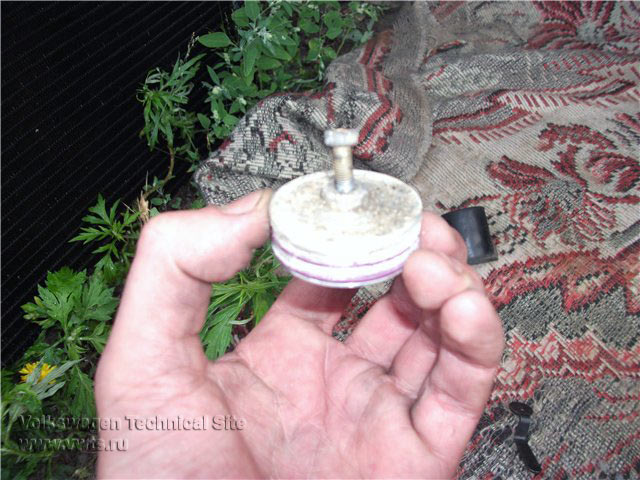
Все, спасибо за внимание, завтра напишу как все заработало, или не заработало))
